Рекомендации, секреты и методики, связанные с подачей и частотой вращения шпинделя
Иногда шпиндель вязнет в материале. Попробуем дать вам несколько советов, как преодолевать подобные ситуации.
#1-#3: Шпиндель вращается недостаточно медленно для имеющегося материала и режущего инструмента
Данная проблема типична при использовании высокоскоростного шпинделя, например, на фрезерных станках с ЧПУ. При обработке твердых материалов или при использовании фрез большого диаметра необходимо снижать частоту вращения шпинделя. Ниже приведены три рекомендации по обеспечению оптимальной работы оборудования:
#1: Используйте фрезы, предназначенные для большой частоты вращения шпинделя и изготовленные из твердосплава вместо быстрорежущей стали.
Фреза должна иметь покрытие (см. статью «Покрытия концевых фрез»), подходящее для работы с высокой скоростью. Титаново-алюминиевый нитрид (TiAlN) и прочие подобные покрытия могут работать в условиях повышенной температуры (на самом деле, они даже лучше работают при высокой температуре), поэтому вы сможете использовать шпиндель на более высоких частотах вращения.
#2: Используйте фрезы с меньшим диаметром. Чем меньше диаметр, тем быстрее режущая кромка должна вращаться относительно обрабатываемой поверхности.
Вы ничего не теряете, поскольку фреза меньшего диаметра позволяет выполнять любые работы, просто операции занимают немного больше времени.
#3: Используйте технологию высокоскоростной обработки (HSM) с соответствующей траекторией движения инструмента при относительно небольшой ширине снимаемого материала.
Это позволяет увеличить не только скорость подачи, но и частоту вращения шпинделя. Чем меньше ширина снимаемого материала в процентном отношении к диаметру инструмента, тем большая частота вращения шпинделя является допустимой. При ширине снимаемого материала 25% от диаметра и глубине снимаемого материала 1xD, можно увеличить скорость вращения шпинделя в 1.88 раза. Проблема может возникнуть только при начале процедуры резки, поскольку при первоначальном проходе может потребоваться максимальная ширина снимаемого материала. В некоторых случаях эта проблема решается путем просверливания отверстия перед началом обработки.
#4-#6 Недостаточная скорость подачи
Вы разобрались с необходимой частотой вращения шпинделя, но она настолько высока, что ваше оборудование не может обеспечить соответствующую скорость подачи (для заданной точности обработки).
Что делать?
Эта проблема менее распространена, чем предыдущая, однако мы также можем дать три совета по ее решению:
#4: Уменьшите частоту вращения шпинделя.
Вы всегда можете снизить обороты шпинделя до минимально возможных значений, либо до уровня минимально допустимой мощности. Фактически, снижение частоты вращения значительно продлит жизнь режущему инструменту за счет снижения тепловыделения и скорости подачи.
#5: Уменьшите количество канавок.
Меньшее число канавок позволяет медленнее проходить через материал, поскольку каждой канавке(каждому зубу) требуется приблизительно одинаковая подача на зуб независимо от общего числа канавок. Уменьшение числа канавок может значительно улучшить качество обработки вязких материалов, поскольку значительно упрощается очистка материала от стружки. Вы можете использовать фрезу с одной канавкой, однако при этом необходимо снизить скорость подачи. Использование фрезы с одной канавкой вместо четырех фактически приведет к четырехкратному снижению скорости подачи.
#6: Используйте фрезу меньшего размера.
Фрезы меньшего размера обеспечивают меньшую подачу на зуб, при этом снижается скорость подачи.
#7 Налипание стружки и поломка фрез при обработке алюминия.
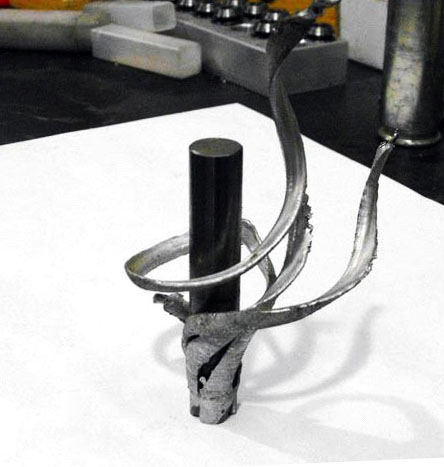
Засорение концевой фрезы наростами алюминия
Это своего рода хитрость, поскольку она не связана с проблемой скорости подачи и частоты вращения. Алюминий имеет тенденцию налипать на кромку режущего инструмента. Когда это происходит, кромка перестает работать, наросты образуются и достаточно быстро, и инструмент полностью перестает функционировать.
Проблема почти всегда связана с недостатком смазки. Даже небольшое количество WD-40 может улучшить ситуацию, а использование правильно подобранной СОЖ, подаваемой поливом или распылением, позволяет легко решить эту проблему.
#8-#14 Я не имею возможности использовать СОЖ, подаваемые поливом или распылением, при обработке алюминия. Что можете посоветовать?
Плохие новости: инструменты имеют ограниченный срок службы. Существует несколько неплохих заменителей СОЖ для предотвращения образования наростов. Главная задача при этом — максимально убирать стружку до того момента, когда она начнет наплавляться на режущие кромки. Приведем несколько способов:
#8: Продувайте место обработки воздухом или используйте глубокий вакуум для удаления стружки.
#9: Избегайте попадания стружки в глубокие полости, из которых ее сложно извлечь.
#10: Старайтесь поддерживать меньшую глубину съема материала — попробуйте использовать диаметр фрезы на 25% или даже меньше.
Это не лучший вариант для продления срока службы инструмента — более предпочтительным вариантом является максимальное распределение нагрузки вдоль режущий кромок фрезы. Однако это не поможет при обработке алюминия без надлежащей смазки.
#11: Прилипание к тонкому листу алюминия.
Тонкий алюминий сцепляется, например, с пенокартоном, поэтому обычно это не является проблемой.
#12: Необходимо соблюдать установленные правила по частоте вращения и подаче.
Хотя я указал вначале, что проблема не связана со частотой вращения и скоростью подачи, однако их уменьшение снизит количество образуемой стружки и позволит получить дополнительное время на ее очистку.
#13: Используйте фрезы с одной или двумя канавками.
Да, фреза с тремя канавками позволит увеличить скорость подачи, однако меньшее число канавок позволит увеличить пространство очистки от стружки и снизит объем образования наростов.
#14: Используйте инструменты со специальным DLC- покрытием.
Покрытие способствует смазке и защищает от образования наростов. Однако необходимо помнить, что покрытие имеет обыкновение внезапно изнашиваться, в результате чего тут же начинается наплавление стружки на режущую кромку.
#15-#18 Работа с глубокими полостями
Речь о глубоких для вашего инструмента обрабатываемых полостях. Такое наблюдается, если вы вынуждены обрабатывать полости со слишком малыми внутренними углами, при этом недостаточно пространства для более крупного инструмента.
Проблема малых фрез связана с их деформацией. Кроме того, что малая фреза не может удалить большие объемы стружки, она имеет слишком большую длину относительно диаметра и склонна к изгибу. Ниже будет описано, почему деформация фрез значительно сокращает их срок службы.
Что значит «большая глубина»?
Твердосплавные держатели для расточки на токарных станках не должны выдвигаться более чем на 6-7 диаметров. Аналогичные правила применимы и к данному случаю. Если фреза выдвигается более чем на 6 диаметров, значит мы обрабатываем глубокую полость, и нам необходимо принимать во внимание несколько дополнительных правил.
Рекомендации по обработке глубоких полостей:
#15: Убедитесь, что внутренние углы максимальны. Большинство компаний хотят максимально удешевить производство.
Зачастую используется минимальный радиус угла полости, однако такой подход не несет никакой функциональной пользы. Обсудите с заказчиком вариант экономии средств за счет использования большего диапазона углов при обработке полостей.
#16: Используйте крупную черновую и малую чистовую.
При обработке можно удалить большую часть материала большой черновой фрезой, а малой (чистовой) фрезой снять небольшое количество оставшегося материала. При этом наблюдается значительное снижение времени, необходимого на обработку.
#17: Обдумайте возможность последовательного сверления, плунжерного фрезерования или обычного сверления углов в глубоких полостях.
#18: Используйте фрезы большего нестандартного диаметра.
Даже небольшое увеличение диаметра фрезы может значительно улучшить ситуацию. Например, можно использовать фрезы с размерами в дюймовой системе вместо метрической или наоборот.
#19 — #23 Работа с глубокими отверстиями
Похожие и даже более серьезные проблемы возникают, когда обрабатываемые отверстия оказывается слишком глубокими по сравнению с их диаметром и, соответственно, по сравнению с диаметром используемого сверла. Приведем несколько способов обработки глубоких отверстий:
#19: Циклически выводите сверло из отверстия.
#20: Используйте сверла с параболическими канавками.
Такая геометрия канавок позволит сверлить более глубокие отверстия в сравнении со спиральными сверлами.
#21: Используйте индивидуальный цикл обработки глубоких отверстий.
#22: Поговорите с заказчиком об изменении конструкции.
Возможно, заказчик согласится увеличить диаметр отверстия или уменьшить его глубину, осознав все экономические преимущества такой модификации.
#23: Используйте СОЖ, подаваемую через шпиндель под давлением.
Такое решение может помочь в удалении стружки из глубоких отверстий.
Высокая скорость съема материала является препятствием для увеличения производительности.
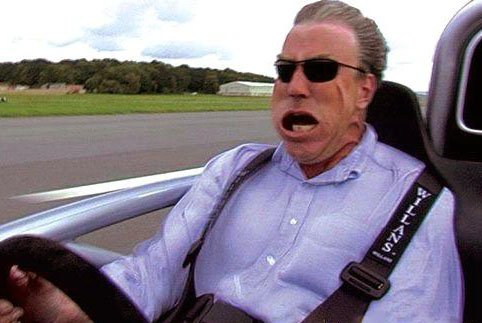
Время — деньги. Вечная нехватка времени — это типичная ситуация для увлеченного делом человека. Увеличение скорости работы позволяет выполнить больше задач за ограниченный период времени.
Вы можете даже не задумываться о том, чтобы ускориться, либо полагаете, что уже работаете на максимальных скоростях, однако, однажды увидев границы возможностей, вы захотите использовать доступные приемы ускорения работы на станке с ЧПУ.
#24-#27 По возможности используйте спиральные сверла вместо концевых фрез
При прочих равных условиях, именно сверла позволяют максимально быстро изготавливать отверстия. Предположим, вам необходимо просверлить отверстие диаметром 1″ и глубиной 1/2″ в алюминии 6061. Если мы будем делать это отверстие высококачественной фрезой из твердосплава диаметром 5/8″, скорость съема материала составит порядка 6.4 кубических дюйма в минуту. Если же использовать вместо этого твист-сверло из твердосплава, скорость составит 32 кубических дюйма в минуту. Даже при использовании сверла из высокопрочной стали этот показатель будет равен 9.6 кубических дюйма в минуту.
Сравнение кажется некорректным, потому что используется сверло большего диаметра? Да, но у нас часто есть под рукой большие сверла. Кроме того, они дешевле фрез аналогичного размера и могут быть заточены после затупления, что позволяет значительно продлить их срок службы.
В данной ситуации воспользуйтесь следующими рекомендациями:
#24: Просверлите отверстия.
#25: Сделайте первоначальное отверстие, требуемое для полости.
Хорошее сверло диаметром 1” сэкономит вам большое количество времени при обработке полости. Просто убедитесь, что смена инструмента не отнимает у вас слишком много времени. Для максимальной экономии времени старайтесь сделать начальные отверстия для всех полостей за один раз без дополнительной смены инструмента.
#26: Высверлите углы полости, что особенно эффективно для глубоких полостей с крутыми углами, при обработке которых может наблюдаться отклонение инструмента.
#27: Рассмотрите вариант последовательного высверливания полости.
Фактически, современным аналогом последовательного сверления является врезное(плунжерное) фрезерование, если ваша САМ-программа поддерживает данную функцию.
#28 Найдите оптимальное соотношение глубины и ширины съема материала [Крайне необходимо придерживаться этой рекомендации!]
Как вы определяете глубину и ширину съема материала (перемещение фрезы между проходами)?
В большинстве станков с ЧПУ используются эмпирические правила, наработанные в течение долгих лет с некоторыми корректировками под конкретные задачи.
С этим связана следующая проблема:
Выбор оптимальной комбинации глубины и ширины снимаемого материала является самым мощным инструментом регулировки частоты вращения, подачи и скорости съема материала.
Тем не менее, многие операторы станков с ЧПУ игнорируют данное преимущество. Сложно представить, но это факт!
Оптимизация этих двух параметров является непростой задачей, поскольку они имеют не только взаимную корреляцию, но и корреляцию со многими другими факторами. Увеличение глубины съема материала приносит пользу инструменту, поскольку наблюдается распределение нагрузки по большей длине канавки, что позволяет уменьшить число проходов при обработке глубоких полостей. С другой стороны, это приводит к большему отклонению инструмента и усложнению процесса удаления стружки. Увеличение ширины съема материала позволяет увеличить скорость подачи и частоту вращения шпинделя, однако существует точка снижения эффективности, которую многие не принимают во внимание, даже при использовании траекторий высокоскоростной обработки. Инструмент начинает вращаться «как сумасшедший», однако удаляет меньше материала, чем при работе с меньшей частотой вращения.
Единственным способом оптимизации этих двух параметров является тестирование множества различных вариантов.
#29 Используйте инструмент с максимально возможным числом канавок для достижения наибольшей скорости съема материала (MRR)
Чем больше число канавок, тем быстрее подача для заданной частоты вращения шпинделя. Для алюминия вы можете использовать инструмент с тремя канавки вместо двух, что даст прирост в скорости, равный 50%. При обработке более твердых материалов можно использовать инструмент, имеющий 5, 6 и более канавок. Иногда это единственный способ получить приличные показатели скорости съема материала для «сложных» материалов при низких оборотах шпинделя.
#30 Используйте фрезы со стружколомом.
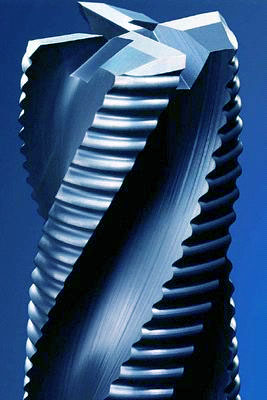
В современном многообразии инструментов экзотических фрезы со стружколомом могут показаться «прошлым веком». Однако, они имеют некоторые значительные преимущества:
- Они могут работать при большей подаче на зуб (соответственно, при больших скоростях подачи) в сравнении с обыкновенными концевыми фрезами, поскольку зубцы вырабатывают стружку меньшего размера, которую проще удалять.
- Они зачастую менее чувствительны к вибрациям. Зубцы привносят дополнительные частоты, которые разрушают резонансы.
#31 Используйте технологию Rest Machining и крупные черновые сверла
Выше мы уже упоминали функцию Rest Machining. Данная функция поддерживается некоторыми CAM-программами и позволяет оборудованию «понять», какое количество материала было удалено при предыдущих операциях. Функция Rest Machining позволяет использовать крупные обдирочные фрезы с последующей чистовой обработкой более мелкими фрезами.
#32 Используйте траекторию высокоскоростной обработки (HSM Toolpath)
Для описания упомянутых траекторий используются термины HSM, спиральное фрезерование, Volumill. Данные траектории не предусматривают попадание сверла в углы. Вместо этого сверло циклически работает в данной области, снимая материал, в результате чего предотвращаются излишние нагрузки на сверло, которые наблюдаются при внезапном попадании его в углы. В результате значительно увеличивается скорость съема материала.
Секрет заключается в поиске оптимального баланса ширины и глубины снимаемого материала для указанных траекторий.
Как продлить срок службы инструментов
#33 Снижение частоты вращения
Совсем необязательно стараться поддерживать скорость съема материала на максимально возможных значениях. Более того, некоторое снижение частоты вращения может значительно продлить срок службы инструмента. Многие операторы снижают частоту вращения на 15% при автоматической работе оборудования для снижения вероятности выхода из строя инструмента.
При этом необходимо снизить скорость подачи на такую же величину, чтобы обеспечить надлежащую подачу на зуб. Никогда не снижайте частоту вращения без снижения скорости подачи.
#34 Используйте правильные программные инструменты для расчета частоты вращения и подачи
Это вполне очевидный совет, но повторюсь: необходимо использовать калькулятор частоты вращения и подачи. Для этого нет универсальных советов. Вы можете прекрасно «слышать», что параметры заданы неверно, однако вы не сможете на слух определить наиболее оптимальную частоту вращения и подачу, что бы вы ни думали, и что бы вам не говорили по этому поводу. Если бы это было возможно, в продаже были бы курсы развития слуха для операторов станков, и все крупные обрабатывающие предприятия заставляли бы операторов проходить соответствующее тестирование. Аналогично в данном случае не работают эмпирические и прочие подобные правила. Конечно, вы можете использовать очень консервативные эмпирические правила для предотвращения выхода из строя инструментов, однако реальная физика настолько сложна, что любые простые эмпирические правила не имеют должного эффекта.
#35 Предотвращение отгиба фрезы
Большинство операторов станков с ЧПУ вполне обоснованно беспокоятся о деформации инструмента и биении. Они знают, что биение значительно сокращает срок службы фрез. Приведенный ниже график визуально демонстрирует его вред:
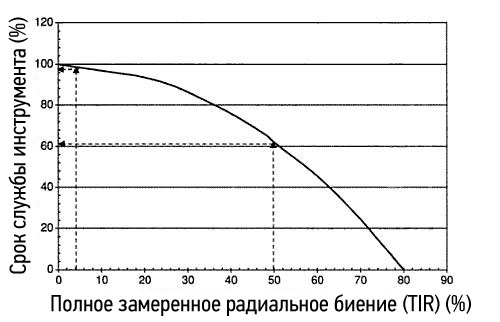
При приближении биения к 50% от подачи на зуб срок службы инструмента значительно сокращается.
Как биение влияет на износ инструментов?
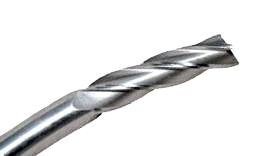
Говоря простыми словами, при его наличии траектория вращения инструмента отклоняется от центральной оси. В результате, он начинает колебаться и некоторые из канавок выполняют большую часть работы, получая дополнительную нагрузку дополнительно к подаче на зуб. При максимизации подачи на зуб с целью достижения максимальной производительности биение достигает критических значений.
А что насчет отгиба?
Отгиб фрезы влияет на срок службы точно так же, как и биение.
Большинство операторов станков не утруждают себя проверкой деформации инструментов, даже если знают о вреде биения и возможных деформациях. При этом они удивляются малому сроку службы инструментов и пониженной точности обработки.
#36 Избегайте трения: не используйте слишком малые скорости или слишком малую ширину съема материала
Приведем наиболее частые ошибки при выборе частоты вращения и подачи. Возможно, вы решите применить ультраконсервативный подход — максимально снизить скорость подачи и использовать крайне малую ширину съема материала. Вы полагаете, что таким образом снизите нагрузку на инструменты, но фактически вы наносите им вред, поскольку они подвергаются постоянному и длительному трению при скоблении материала. Скобление наблюдается в случае слишком малой подачи на зуб. Если мы посмотрим на режущую кромку и стружку под микроскопом, мы увидим следующую картину:
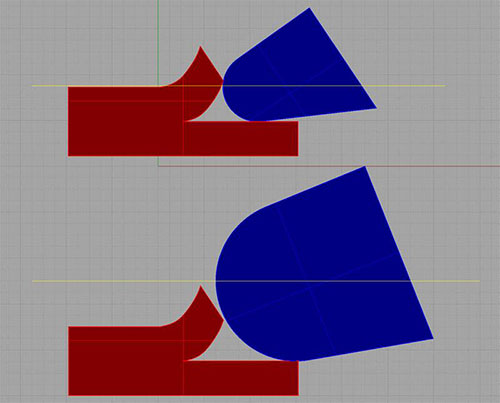
На верхнем рисунке резец работает нормально, поскольку кромка заходит под стружку. На нижнем рисунке наблюдается трение, поскольку стружка слишком мелкая, и режущая кромка не заходит под нее.
На верхнем рисунке резец работает нормально, поскольку кромка заходит под стружку. На нижнем рисунке наблюдается трение, поскольку стружка слишком мелкая, и режущая кромка не заходит под нее. В результате, инструмент скользит вдоль материала, а не снимает его, а повышенное трение вызывает чрезмерную генерацию тепла, что является причиной перегревания инструмента.
Существует еще один негативный вредный фактор, называемый «радиальным истончением стружки». Когда ширина съема материала меньше радиуса инструмента, толщина стружки оказывается меньше ожидаемой. Это наглядно продемонстрировано на следующем рисунке:
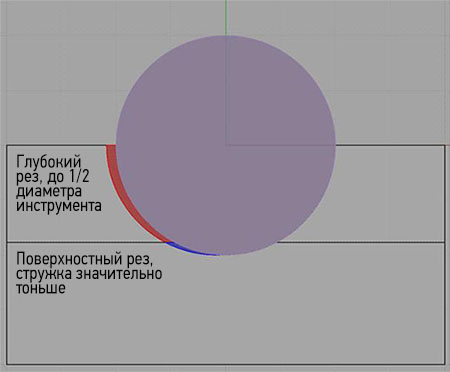
Радиальное истончение стружки наблюдается в случае, когда ширина съема материала становится меньше радиуса инструмента.
Чем меньше ширина съема материала, тем больше проявляется эффект истончения стружки. Именно поэтому уменьшение скорости подачи и ширины съема материала может привести к стремительному увеличению трения при снижении подачи на зуб.
#37: Не используйте слишком малый рез при работе с термообработанными материалами.
Вам требуется, чтобы режущая кромка работала максимально быстро с твердым верхним слоем материала? Этого можно добиться увеличением подачи на зуб и ширины съема материала.
#38: Избегайте повторного реза стружки, удаляйте её.
Убедитесь, что используется жидкостное охлаждение, достаточное для очистки реза от стружки, выдувайте стружку. В некоторых случаях операторы снижают расход СОЖ вследствие отсутствия у станка защитных ограждений и желания избежать беспорядка. В данном случае необходимо подавать СОЖ распылением, поскольку жидкость только покрывает стружку в резе, и вы ее не видите.
#39: Выбирайте траекторию движения инструмента, позволяющую наиболее мягко входить в материал и выходить из него.
Наибольший износ инструмента происходит в момент начала обработки материала. В некоторых случаях даже может произойти «забивание» режущей кромки, особенно при работе с твердыми материалами. В данном случае необходимо использовать траектории с плавным входом в материал. Избегайте резкого входа инструмента в материал. При этом возможны следующие варианты:
— Обеспечивайте относительно плавный угол входа
— Обеспечивайте вход в материал по спирали
— Используйте сверла с механическим креплением сменных многогранных пластин, имеющие размеры, достаточные для формирования первоначального отверстия.
— При профилировании и выравнивании поверхности обрабатывайте материал по дуговой траектории.
См. также:
> Резка заготовок на станке
> Как выбрать шпиндель