Съем, подача и скорость вращения. Основные принципы для начинающих
Что такое скорость подачи и частота вращения (скорость) шпинделя и какую роль они играют при фрезеровании?
Есть ряд основных принципов и терминов, используемых фрезеровщиками, с которыми должен быть знаком каждый специалист.
Параметр «скорость шпинделя» относится к частоте вращения шпинделя, выраженной в об/мин (обороты в минуту). В ходе серии экспериментов, проведенных на раннем этапе развития фрезерования, было выявлено, что частота вращения шпинделя является одним из наиболее значимых факторов, определяющих срок службы режущего инструмента. Использование инструмента при чрезмерно высокой частоте вращения вызывает выделение избыточного количества тепла (есть и другие причины выделения избыточного тепла), что приводит к размягчению материала инструмента и, в конечном итоге, вызывает затупление его режущей кромки. Возможно, скоро появится статья, в которой обсудим способы продления срока службы инструмента, но пока считайте, что частота вращения шпинделя является наиболее существенным фактором, влияющим на срок службы.
Параметр «подача» относится к скорости подачи, измеряемой в различных единицах измерения перемещения в единицу времени (дюймы в минуту или миллиметры в минуту, в зависимости от того, используете ли вы метрическую или британскую систему мер и весов). Скорость подачи влияет на скорость съема материала. Скорость съема материала — это параметр, измеряющий то, насколько быстро в кубических единицах измерения ваша фреза снимает стружку — для большинства фрезеровщиков — чем быстрее, тем лучше, пока это не создает проблемы (см. также «Как выбрать фрезы»).
Наиболее часто возникающей проблемой является разрушение инструмента или образование сколов на режущей кромке, в случае если скорость подачи слишком высока.
См. также: > Советы по выбору скорости и подачи для шпинделя
Я — новичок. Что будет, если я буду работать на станке с очень медленной скоростью?
Существует распространенное заблуждение о том, что вы можете «нянчиться» с инструментом для того, чтобы снизить его износ. Просто используйте шпиндель на низкой частоте вращения и малую скорость подачи, и при этом вы ничего не сломаете, правильно? Не совсем так. Металл — это материал, не прощающий ошибок. Пластмассы, дерево, а также другие мягкие материалы тоже могут вызывать проблемы, связанные с неправильно установленными параметрами частоты вращения шпинделя и скорости подачи, но металл является самым чувствительным материалом.
Вот ряд примеров того, что может случиться, если скорость подачи и частота вращения шпинделя слишком малы:
- Если вы слишком сильно снизите частоту вращения шпинделя относительно скорости подачи, вы заставите канавки вашей фрезы принимать на себя слишком много материала. Концевая фреза (см. также «Применение однозубых концевых фрез») вводится в заготовку слишком быстро, а стружка становится слишком большой. Таким образом вы можете очень легко сломать фрезу.
- Если вы слишком сильно снизите скорость подачи относительно частоты вращения шпинделя, вскоре произойдет следующее: канавки фрезы начнут стирать и полировать заготовку вместо того, чтобы снимать стружку. Многие фрезеровщики скажут вам, что самый быстрый способ затупить фрезу — это использовать ее на шпинделе, вращающемся в обратном направлении, и сделать проход. Но низкая скорость подачи также создает такой эффект. Мы обсудим это более подробно в статье, посвященной скорости подачи и частоте вращения, но достаточно будет отметить, что использование фрез при низкой скорости подачи также плохо сказывается на них, как и работа на высокой скорости подачи, если не хуже.
Хорошо, я понял — существуют оптимальные значения скорости подачи и частоты вращения.
Да! Совершенно верно, для каждой операции по фрезерованию существует оптимальное значение. Это не жесткая точка, которую нужно обязательно достичь, но, в тоже время, диапазон допустимых значений не очень велик, поэтому возможны проблемы, если вы выйдете далеко за его пределы. Чем сложнее для обработки фрезеруемый материал, тем меньше диапазон оптимальных параметров и тем больше износ инструмента. Как только вы узнаете, где находятся оптимальные значения, вы сможете настраивать параметры резания в пределах нужной области значений для того, чтобы максимально увеличить скорость съема материала, качество обработки поверхности заготовки или срок службы инструмента. Фактически, вы можете максимально увеличить любые два параметра из трех, но только не все три сразу.
Давайте рассмотрим оптимальные значения для различных параметров, а также опасные зоны:
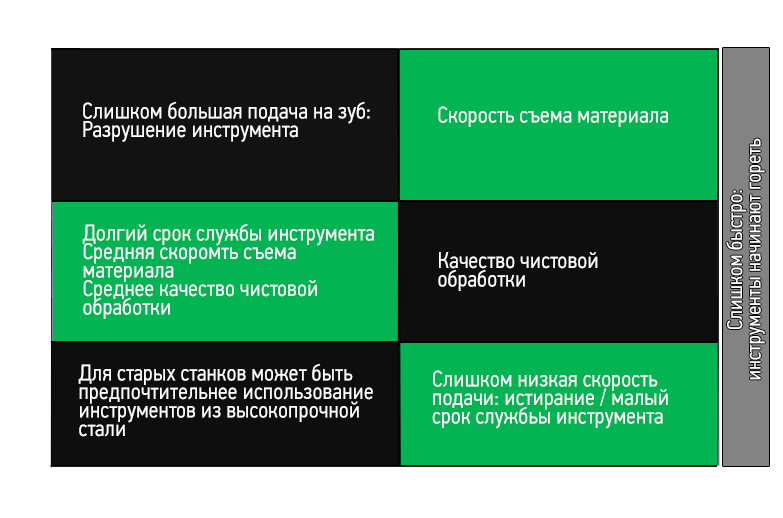
Данная таблица является условной, что означает отсутствие каких-либо пропорций или шкалы измерения. Следует рассматривать только положение отдельных областей относительно друг друга, а также относительно того, насколько высокими или низкими являются частота вращения шпинделя и скорость подачи. Давайте рассмотрим отдельные участки с надписями (слева направо, сверху вниз):
Слишком большая подача на зуб: как уже обсуждалось ранее, когда вы ведете фрезу слишком быстро при заданной частоте вращения шпинделя, вы, скорее всего, сломаете инструмент. Чем больше вы превышаете надлежащую скорость подачи, тем больше вероятность поломки. Вы всегда будете ломать инструмент в какой-то момент. Представьте абсурдную ситуацию, при которой частота вращения шпинделя равна нулю, а вы быстро подвели фрезу к заготовке. Бац! Сломали еще один инструмент.
Скорость съема материала: Оптимальным вариантом для достижения высокой скорости съема материала является максимальная частота вращения шпинделя, при которой не происходит пережог инструмента, и максимальная подача, при которой не происходит разрушение инструмента. Если вы занимаетесь фрезерованием в промышленных масштабах, это тот момент, который принесет вам прибыль за счет более быстрого выполнения работ по сравнению с конкурентами.
Слишком быстро: Слишком высокая частота вращения шпинделя вызывает выделение избыточного количества тепла, что приводит к размягчению материала инструмента и его скорому затуплению. Однако существуют исключения и смягчающие обстоятельства, о которых мы поговорим в следующих разделах.
Долгий срок службы инструмента: Небольшое снижение частоты вращения шпинделя, а также уменьшение скорости подачи чуть ниже значений, необходимых для достижения максимальной скорости съема материала, обеспечивают долгий срок службы инструмента. Ниже мы более подробно рассмотрим формулы Тейлора, касающиеся срока службы инструмента, а сейчас достаточно будет сказать, что снижение частоты вращения шпинделя важнее, чем снижение скорости подачи, но в данном случае и то, и другое может помочь.
Качество чистовой обработки: Снижение скорости подачи при сохранении частоты вращения шпинделя снижает подачу на зуб и позволяет достичь более качественной чистовой обработки поверхности заготовки. Существуют определенные ограничения, главное из которых связано с ситуациями, когда вы в какой-то момент слишком сильно уменьшаете скорость подачи, поэтому ваши инструменты начинают истираться и срок их службы значительно сокращается вследствие выделения избыточного количества тепла ввиду износа.
Старые станки: Итак, частота вращения шпинделя значительно снизилась вдобавок к снижению скорости подачи. Вероятно, вы работаете на старом станке, на котором нет возможности подобрать те скорости, которые вам нужны для успешного использования твердосплавных инструментов. Возможно, вам нужно перейти на инструменты из высокопрочной стали. Многих удивляет факт того, что есть участки в диапазоне параметров скорости подачи и частоты вращения, на которых инструменты из высокопрочной стали могут превзойти твердосплавные по надежности, но с учетом возможностей вашего станка и обрабатываемого материала.
См. также: > Как выбрать режущий инструмент
Слишком низкая скорость подачи: Как обсуждалось ранее, слишком медленная подача приводит к трению фрезы о заготовку вместо резания, что является причиной значительного сокращения срока службы инструмента. Этого нужно избегать.
Теперь, когда вы знаете об оптимальном распределении параметров обработки, у вас будет более четкое представление о том, каким образом нужно регулировать подачу и частоту вращения шпинделя для получения желаемых результатов.
Как выбрать шаг перемещения фрезы между проходами?
Одним из фундаментальных параметров при работе на станках с ЧПУ или 3D-фрезерованию в частности, является шаг перемещения фрезы между проходами. Не будет преувеличением, если назвать данный параметр самым важным в определении уровня качества производимых деталей. Оператор может выбрать данный параметр по ощущению, основываясь на прошлом опыте, либо провести расчеты и вычислить оптимальное значение параметра, что позволит ему получить требуемый результат обработки. Как правило, новички не имеют достаточного опыта и не знают, каким образом нужно производить расчеты, поэтому им требуется некоторое время, чтобы достичь интуитивного понимания для определения оптимального шага фрезы между проходами.
Содержание данной статьи сосредоточено преимущественно на траекториях движения фрезы при 3D-фрезеровании, поэтому примем, что используем в работе сферическую фрезу. Как только вы поймете основные принципы работы со сферической фрезой, вам будет легко применить их к работе с концевыми фрезами с плоским торцом, а также с грибковыми фрезами. Вместо того, чтобы выводить формулы, которые вряд ли заинтересуют большую часть читателей, мы постараемся обозначить общие правила.
- Определение шага перемещения фрезы между проходами
Траектории движения фрез у большинства станков с ЧПУ основаны на принципе смещения траектории движения инструмента на каждом проходе относительно предыдущего прохода на определенное расстояние; данное смещение обычно называют перемещением фрезы между проходами. Большая часть CAM-программ, включая MeshCAM, использует две траектории движения инструмента, в частности, со следующими видами сдвига — растровая траектория движения инструмента (иногда называемая зигзагообразной траекторией), а также контурный сдвиг.
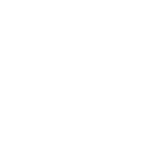
Траектория движения инструмента с контурным сдвигом
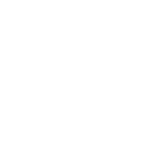
Растровая или зигзагообразная траектория движения инструмента Смежные участки траектории движения инструмента отделены друг от друга шагом перемещения фрезы между проходами, выбранным оператором.
- Образование волнообразных кромок
Изображения, представленные выше, показывают, как выглядит траектория движения инструмента на виде сверху, но вид сбоку четко указывает на основной побочный эффект выбора перемещения фрезы между проходами — образование волнообразных кромок.
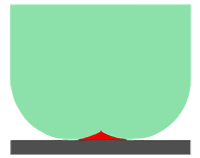
Волнообразная кромка,
отмеченная красным, ме-
жду смежными
проходами фрезы
Область, выделенная красным цветом — это не снятый остаток материала, вызванный смещением траектории движения инструмента. Важно понимать, что данное явление является негативным; такие остатки материала не учитываются CAD-программой и их, возможно, придется удалить после фрезерования путем шлифовки или полировки. Как правило, операторы станов с ЧПУ почти всегда стараются уменьшить образование волнообразных кромок всеми возможными способами; люди потратили огромное количество времени в попытке создания алгоритмов траектории движения инструмента, которые позволили бы минимизировать образование волнообразных кромок.
- Волнообразные кромки и перемещение фрезы между проходами
При более глубоком изучении изображения, показанного выше, станет ясна связь между высотой волнообразных кромок и значением шага перемещения фрезы между проходами — при увеличении одного параметра также увеличится и другой. На изображениях, представленных ниже, мы использовали шаг перемещения фрезы между проходами, равный 1/10, 1/5, и 1/3 диаметра инструмента, чтобы наглядно показать данную взаимосвязь. Если перенести эти показатели на реальные цифры, то они будут соответствовать шагу перемещения фрезы между проходами, равному 0,012, 0,025, и 0,042″ соответственно — для сферической фрезы диаметром 0,125″.
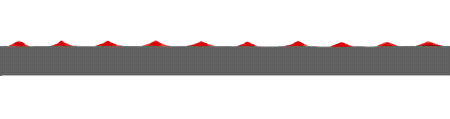
Шаг перемещения фрезы между проходами = 1/10 диаметра фрезы
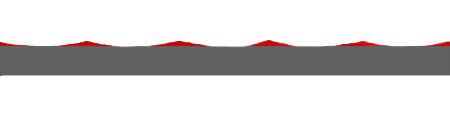
Шаг перемещения фрезы между проходами = 1/5 диаметра фрезы
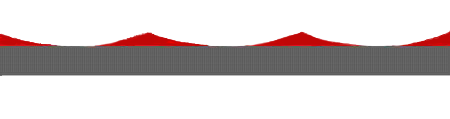
Шаг перемещения фрезы между проходами = 1/3 диаметра фрезы
Как вы можете видеть, изменения в качестве являются настолько значительными, что у вас может появиться соблазн всегда использовать минимально возможный шаг перемещения фрезы между проходами.
Скорость против качества
Неудивительно, что вам придется чем-то пожертвовать, если вы хотите использовать действительно малый шаг перемещения фрезы между проходами. В подобном случае вы меняете время на качество — вы теряете в скорости обработки при использовании малого шага перемещения фрезы между проходами или жертвуете качеством в угоду уменьшения времени обработки. Это легко понять, если принять в расчет следующий факт: если вы снизите шаг перемещения фрезы между проходами в два раза, то общая длина траектории движения инструмента увеличится приблизительно вдвое. Вопрос состоит в следующем: «Удвоит ли уменьшение шага перемещения фрезы между проходами вдвое качество обработки заготовки?»
Золотая середина
Получается, что соотношении времени и качества обработки существует точка падения эффективности. Ниже находится график, показывающий соотношение между высотой волнообразных кромок и шагом перемещения фрезы между проходами, который наглядно демонстрирует данный эффект. График построен для инструмента с условным диаметром 1.0, поэтому его легко масштабировать относительно инструмента любого другого диаметра, который вы используете.
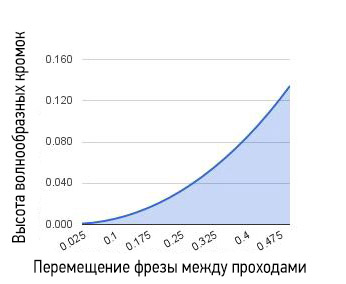
График, показывающий отношение высоты волнообразных кромок к перемещению фрезы между проходами
Важно отметить форму кривой на графике — она становится более пологой в той точке, когда шаг перемещения фрезы между проходами становится ниже приблизительно 1/8 диаметра инструмента. Это означает, что при опускании ниже указанной точки, вы будете тратить больше времени на работу без пропорционального увеличения качества обработки. Это может быть оправдано, если вы изготавливаете стальную форму для литья под давлением, но, прежде чем работать при таких параметрах, вам нужно убедиться их целесообразности.
Волнообразные кромки и диаметр инструмента
Есть еще один момент, который мы можем почерпнуть из расчетов, стоящих за графиком, показанным выше — при определенном шаге перемещения фрезы между проходами использование инструмента большего размера обеспечит образование кромок меньшего размера. Это означает, что вы можете получить обработку лучшего качества «бесплатно», если у вас есть возможность использовать инструмент большего размера. Очевидно, что данная схема будет работать только в том случае, если инструмент большего размера соответствует геометрии заготовки. Но это лишь один из нескольких беспроигрышных вариантов, когда мы действительно можем получить лучший результат, если такой способ подходит для геометрии заготовки.
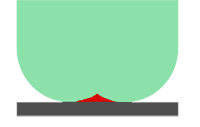
Волнообразная кромка при использовании инструмента небольшого размера.
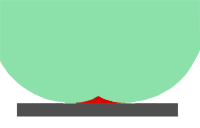
Обратите внимание на меньший размер волнообразной кромки при использовании инструмента большего размера даже при сохранении постоянного шага перемещения фрезы между проходами.
Не забывайте об обрабатываемых материалах
Прежде чем вы определите требуемое вам значение шага перемещения фрезы между проходами для получения волнообразной кромки высотой 0,0001″, подумайте о том, что вы будете обрабатывать — дерево, модельные материалы, алюминий, сталь и т.д. Могу сказать, что в большинстве случаев за 10 минут шлифования деревянной заготовки вы сможете достичь нужного качества чистовой обработки, получение которого заняло бы у вас лишний час или два при использовании фрезы. То же самое касается и модельных материалов, чью чистовую обработку можно достаточно быстро выполнять вручную, чтобы не увеличивать время машинной обработки вдвое для получения аналогичного результата. Если вы фрезеруете сталь или другие твердые материалы, тогда, возможно, стоит оставить фрезе больше тяжелой работы.
Второй характеристикой обрабатываемого материала, которую необходимо учитывать, является то, какие размеры могут выдерживаться на деталях. Например, при работе с МДФ невозможно выдержать размер 0,01″, а при работе с металлом — возможно. Если материал, который вы обрабатываете, не позволяет выдерживать размер, меньший высоты волнообразной кромки, тогда вам не стоит снижать шаг перемещения фрезы между проходами; таким образом вы только зря потратите время, не добившись лучшего качества обработки.
Помните о том, каким станком с ЧПУ вы пользуетесь
Плохой работник может обвинять свое оборудование в неудовлетворительных результатах работы, но мы должны оставаться реалистами в отношении возможностей используемых станков. В частности, следует понимать, в течение какого срока ваш фрезерный станок или роутер может работать без возникновения неполадок. Некоторые начинают с небольшого фрезерного станка настольного типа, который сам по себе неплохой, но, несмотря на это, не может проработать и нескольких часов, не останавливаясь или не начав барахлить по той или иной причине, что приводило к выходу из строя какой-либо детали, которую ждать ждать полдня. Если вы работаете на подобном станке, вам стоит подумать о том, чтобы установить максимально возможный шаг перемещения фрезы между проходами — скорее с учетом времени обработки, а не ее качества.
Общие правила
Мы рассмотрели замечательный набор изображений, но у вас, возможно, еще остался вопрос: «Так какой же шаг перемещения фрезы между проходами мне использовать?» Ниже приведен ряд рекомендаций:
- Шаг перемещения фрезы между проходами должен иметь значение от 1/3 до 1/10 диаметра инструмента;
- Используйте больший шаг перемещения фрезы между проходами в диапазоне от 1/5 до 1/3 диаметра инструмента для мягких материалов, которые не позволяют выдерживать малые размеры;
- Используйте меньший шаг перемещения фрезы между проходами в диапазоне от 1/5 до 1/10 диаметра инструмента для твердых материалов или материалов, из которых можно изготавливать ответственные детали, например, металл или ювелирный воск;
- Используйте инструмент максимального размера, который позволит вам проводить обработку с учетом необходимой геометрии (см. также «Концевые твердосплавные фрезы: Геометрия»).