Для чего использовать однозубую (одноперую) концевую фрезу?
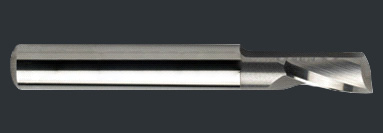
Среди современного разнообразия режущего инструмента, порою встречаются действительно странные изделия, физика работы которых не сразу понятна, поэтому выбрать фрезу для станка бывает нелегкой задачей. Так, многие операторы ЧПУ знают, что чем больше режущих кромок, тем выше производительность, в то же время некоторые материалы, например алюминий, требуют меньше режущих кромок – обычно две или три. И если это правило развить дальше, то тогда целесообразно ли было бы использовать однозубую концевую фрезу? Есть ли такие задачи, для которых подойдет минимально возможное количество зубьев?
Если ответить одним словом, то да. Давайте поговорим, почему это так. Причина, по которой желательно использовать меньшее количество зубьев, связана с поведением стружки. Так, при обработке алюминия формируется стружка большего размера, в сравнении с другими материалами. Это связано с тем, как сворачивается материал, а также рядом других факторов. Пространство, создаваемое стружечными канавками такой концевой фрезы – это то место, по которому стружка удаляется в процессе резки. И если этого места будет недостаточно, то может произойти повреждение режущего инструмента. Именно поэтому при обработке алюминия стараются использовать инструмент с меньшим числом зубьев и, соответственно, с большим пространством для удаления стружки.
Это проблема производительности, когда большее количество стружечных канавок может быть более продуктивным, может быть связана с двумя факторами: скоростью удаления материала (MRR) и классом обработки поверхности.
Один из этих факторов имеет большое значение для черновой обработки (MRR), и один, очевидно, имеет большее значение для вашей финишной обработки. То, что связано с этим фактором, я называю «Тиранией поверхностной скорости».
Оставим в стороне проблему стружечных канавок и поговорим о процессе резания однозубым режущим инструментом на станке. На самом деле это очень просто и помогает пролить свет на то, что происходит в процессе резания. Для каждого обрабатываемого материала есть своя скорость резания, рекомендованная производителем. Это рекомендация в значительной мере связана с работой на максимальной скорости вращения (или заготовки на станке) без ущерба для срока службы режущего инструмента. Лимитирующим фактором является скорость отведения тепла. Карбид вольфрама может противостоять тепловому потоку, по сравнению с быстрорежущей сталью перед началом размягчения. Если материал, из которого сделан инструмент, размягчается, режущий край инструмента быстро притупляется. Итак, если вы хотите, чтобы инструмент мог выдерживать большее количество тепла, вам необходимо использовать твердосплав вместо быстрорежущей стали. Поскольку мы не можем преодолеть скоростной лимит, нам приходится подбирать другие параметры. Итак, давайте предположим, вы запустили инструмент на максимальной скорости. Чем быстрее скорость резания, тем выше температура инструмента и тем быстрее он притупляется. Как еще мы можем получить более высокие скорости удаления материала? Ответ заключается в том, что мы размещаем больше режущих кромок по окружности режущего инструмента, чтобы при вращении фрезы мы получаем намного больше точек резания. При заданной скорости резания 4-канальная концевая фреза может давать четыре точки реза при данной подаче на зуб, в это время для двух стружечных канавок их будет 2, при той же толщине стружки. Таким образом, четыре стружечных канавки могут иметь в два раза большую скорость удаления материала (MRR). Именно поэтому мы видим, что резаки с большим числом канавок становятся популярными в сложных материалах, которые допускают медленные скорости резания. Таким образом, можно повысить производительность обработки для таких материалов.
Теперь о качестве обработке поверхности. Уже было сказано, что использование большего количества зубьев равноценно увеличению скорости шпинделя. Материал не различает разницы между резанием дважды за оборот двухзубой фрезой при 6000 об/мин или четырехзубой фрезой на 3000 об/мин.
Следовательно, переход от фрезы с двумя зубьями к фрезам четырьмя зубьями можно приравнять к удвоению скорости вашего шпинделя. При увеличении скорости при той же подаче на зуб улучшается качество обработки поверхности (по-крайней мере, пока фреза еще режет, а не скоблит, см. ниже). Если нет необходимости использовать двузубую концевую фрезу для хорошего удаления стружки, например для обработки алюминия без существенного заглубления, можно использовать даже четырехзубые фрезы.
Всё больше данных, что для использования концевой фрезы с одним зубом нет задачи?
Тогда пришло время, чтобы изучить случаи для использования таких фрез. Перед тем как это сделать, надо рассмотреть феномен как «скобление», когда стружка становится слишком мелкой. Здесь достаточно сказать, что если вы перемещаете инструмент слишком медленно, то стружка становится слишком тонкой по отношению к режущей кромке настолько, что та не может быть начисто удалена режущей частью инструмента. Фреза рвет стружку и даже может проскальзывать на ней несколько оборотов, прежде чем она собьётся в комок и будет удалена.
Теперь давайте рассмотрим пример с ЧПУ станком. Допустим шпиндель может вращаться со скоростью 24000 об/мин, но не менее 12000 об/мин. Когда мы режем алюминий, первое что мы обнаруживаем это необходимость использования твердосплавного инструмента, желательно с хорошим покрытием фрезы. Когда мы начинаем работать с определенными скоростями вращения и подачи и мы обнаруживаем, что нам понадобятся довольно высокие скорости подачи при этих скоростях вращения. Так, например концевая фреза 6 мм дюйма может работать при скорости вращения шпинделя 24000 об/мин и скорости подачи 6000 мм/мин. Теперь в зависимости от станка мы можем столкнуться с проблемой.
Что можно сделать, если ваш станок не может обеспечить такую скорость подачи?
Ответ состоит в использовании фрезы с одним зубом, поскольку она вдвое снижает скорость подачи без трения. Так что есть случай, когда такая фреза может выручить, если станок не может обеспечить требуемую скорость подачи, чтобы не отставать от того количества и поддерживать достаточную нагрузку на кромку. Другой случай: всегда, когда мы получаем преимущество в дополнительном удалении стружки – это большой плюс. Есть много сценариев, где важно хорошее удаление стружки:
- вы режете пластину из очень вязкого алюминия, в этом случае обязательно используется двузубая фреза вместо трехзубой. В тоже время может оказаться выгоднее выполнить работу фрезой с одним зубом.
- вы используете микрофрезу, которые имеют худшую геометрию фрезы в сравнении с фрезами большего размера, это никак не исправить – это физика. Вы можете сделать режущую кромку максимально острой, но в микромасштабе оно все равно будет оставаться недостаточно острым. Кроме того значительно выше тенденция к свариванию стружки и пространство для удаления стружки является проблемой при микрообработке. Перейдите на фрезу с одним зубом. Большинство рекомендует такой подход уже долгое время и даже выпускает специальные однозубые фрезы со специальной сбалансированной геометрией для высоких оборотов.
- Вам необходимо сделать глубокий рез или фрезеровать небольшую глубокую выемку и часто бывает очень трудно удалить стружку из отверстия, и она забивает его. Идеально, если вымывать стружку СОЖ, но, если это не поможет, попробуйте использовать фрезу с одним зубом.
- Вы делаете глубокую фрезеровку трехмерного профиля во время, которого фреза опускается во множество узких мест с минимальным зазором.
Третий вариант: некоторые материалы лучше обрабатываются фрезами с одним зубом. Как правило, это мягкие материалы, которые легко царапаются. Потому при обработке таких материалов необходимо обеспечить удаление стружки. Мягкие материалы – это не только мягкие металлы, но и пластмассы. Также можно получить заметный прирост производительности при работе с некоторыми видами дерева (мягкие породы и МДФ). Использование однозубой фрезы может помочь в процессе резания слоистых листовых материалов (композитных панелей), однако различия в процессе резания незначительные и как правило проявляются на высоких оборотах шпинделя.
Меньшее количество стружечных канавок означает меньшее количество повторного реза по стружке, в результате получается лучшее качество обработки поверхности.