Твердосплавные концевые фрезы: геометрия
Почему некоторые концевые фрезы стоят дороже, чем другие и стоит ли на них тратить деньги?
В какой-то момент у каждого, кто занимается металлообработкой, появлялся этот вопрос - как выбрать фрезы для станка, которые будут отвечать моим нуждам? Многие работают только с режущим инструментом конкретной фирмы производителя. Рекомендованные производителем параметры скорости вращения и подачи инструмента зависят от обрабатываемого материала и типа резания, и они заметно отличаются. Разные торцевые фрезы действительно, работают по-разному, и их стоимость может значительно отличаться.
В данной статье мы рассмотрим три основных фактора, от которых зависит работа фрезы: сплав из которого она сделана, ее геометрия, покрытие фрезы.
Класс и качество твердого сплава
Начнем с материала, из которого изготавливаются концевые фрезы. Не смотря на то, что большинство производителей называет материал «сплошной карбид», на самом деле это «цементированный карбид». Не думаю, что производители, таким образом, пытаются ввести в заблуждение, просто маркетинг не может не использовать громких прилагательных и вы, как покупатель, можете сказать, что их фрезы «сплошные» и в конструкции фрез нет твёрдосплавных режущих вставок. На самом деле, материал из которого изготовлены такие фрезы, не является сплошным однородным металлом, это композит, состоящий из карбида вольфрама (соединение вольфрама и углерода в равных долях) и связующего вещества (как правило, кобальта). Непосредственно за процесс резания, в этой смеси, отвечает карбид вольфрама. В свою очередь, качество такого карбида вольфрама зависит от того сколько его зерен содержится в смеси, по сравнению со связующим материалом. Дешевый цементированный карбид содержит больше связующего, чем дорогого карбида вольфрама. Качество же самого карбида вольфрама зависит от способа его производства и размера зерен.
Если вы задаетесь вопросом как выбрать режущий инструмент, возьмите на заметку - при описании лучших сортов карбида, используют термины «субмикронный» или «микрозернистый», и в этом есть простая логика – чем более мелким будет зерно, тем больше таких зерен будет в смеси, в сравнении со связующим материалом. Для простоты понимания, представьте себе два одинаковых ящика заполненных шарами. Один ящик заполнен большими шарами, а другой маленькими шарами. Начнем заполнять ящики водой. В итоге, в ящике, заполненном шарами большего размера, из-за менее плотной их упаковки, окажется больше воды, чем в ящике, заполненном шарами меньшего размера. Теперь представьте, что шары в ящике это зерна карбида вольфрама, а вода это связующий материал. Ниже представлена иллюстрация нашего мысленного эксперимента.
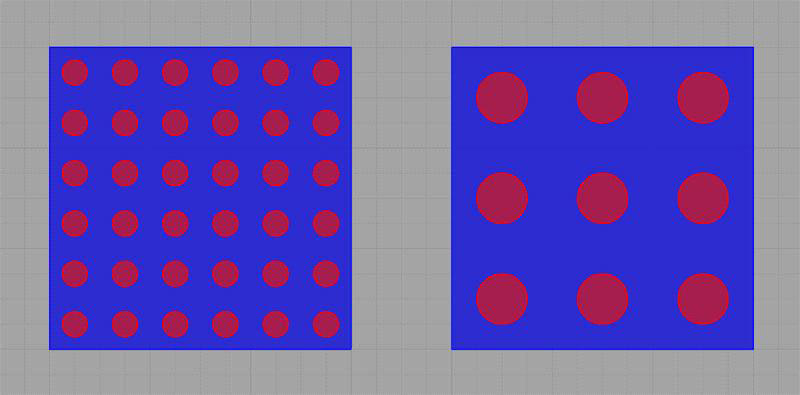
Концевые фрезы, выполненные из материала содержащего маленькие зерна карбида вольфрама лучше, так как содержат больше карбида вольфрама и меньше связующего материала.
Стоит, однако, помнить, что составы цементированного карбида, содержащие более мелкую фракцию карбида вольфрама дороже в производстве, особенно если при производстве соблюдаются высокие стандарты качества, а потому, покупая такие фрезы, мы получаем лучшую производительность инструмента - он дольше остается острым, потому что содержит больше высокопрочного карбида вольфрама чем, относительно, более мягкого связующего.
Геометрия

Значительное влияние на производительность фрезы оказывает ее геометрия. Различные экзотические геометрии служат для выполнения специальных задач, в данной статье мы не будем рассматривать все многочисленные вариации. Рассмотрим только несколько наиболее распространенных примеров.
Начнем с обычной концевой спиральной фрезы, она может быть выполнена с малым углом наклона зубьев, большим углом наклона зубьев, может быть предназначена для черновой и чистовой обработки, так же может иметь переменный шаг. Что же это все значит для оператора ЧПУ?
Термины «большой угол наклона» или «малый угол наклона» относятся к углу наклона режущей кромки фрезы.
Представьте угол между кромкой спирали стружечной винтовой канавки и плоским концом стандартной концевой фрезы: малый угол наклона режущей кромки – значение угла равно 35° или менее, большой угол наклона – значение угла более 35°. Хорошим компромиссом, между фрезами для черновой и финишной обработками, являются инструменты с углом наклона зубьев – 38°. Максимально возможный угол наклона зубьев имеют прямозубые фрезы, которые применяются для контурной обработки и если вы знакомы с недостатками таких фрез, то наверняка вам будет интересно узнать про преимущества и недостатки концевых фрез с малым и большим наклонов зубьев.
Преимущества фрез с большим наклоном кромки:
- режущее усилие направлено в большей степени вертикально, чем горизонтально, что уменьшает отклонение инструмента;
- быстрое удаление стружки из зоны резания;
- положительный передний осевой угол способствует лучшему сдвигу материала и уменьшает усилие резания, что позволяет работать с большими скоростями подачи, при меньшей мощности;
- ядро инструмента толще, благодаря форме, следовательно, фреза прочнее.
Концевые фрезы с крутой спиралью обычно применяются для обработки твердых материалов, поскольку они лучше истираются, в тоже время такие фрезы вполне можно использовать и для обработки алюминия.
Самым большим недостатком концевых фрез с крутой спиралью является то, что им свойственны вибрации, они могут закусывать металл. При работе с мягкими материалами фрезы могут выпадать из держателя (в сравнении с фрезами с пологой резьбой). Обрабатываемая поверхность также может быть плохо обработанной из-за малого шага таких фрез.
Преимущества фрез с малым наклонов кромки:
- меньшая вероятность вибрации;
- показывают лучшую производительность при работе с мягкими материалами;
Недостатки таких фрез заключаются, в том, что при работе с твердыми материалами, режущий инструмент работает при низких скоростях подачи, а, следовательно, с низкими скоростями удаления материала.
Концевые фрезы с переменным шагом считаются самыми современными. Основная идея таких фрез заключается в изменяемом шаге спирали вдоль ее длины. Режущие кромки могут быть неравномерно разнесены, и угол наклона стружечной винтовой канавки может изменяться вдоль длины фрезы. Цель создания переменной спирали – борьба с вибрациями, так как вибрация является резонансным эффектом, а потому переменный шаг помогает разрушить резонанс режущих кромок взаимодействующих с обрабатываемым материалом.
Переменное расстояние между режущими кромками, позволяет им не создавать ритмическую нагрузку на инструмент. Для того чтобы еще уменьшить такую возможность большинство конструкций концевых фрез сделаны не только с переменным шагом режущих кромок, но с переменным углом их наклона. Такая комбинация означает, что режущие кромки одинаково разнесены, но расстояние между ними в каждой точке длины фрезы уменьшается. Излишне говорить, что существует множество различий в конструкциях производимых различными производителями и множеством патентов.
Существует также другая разновидность экзотической геометрии, которая включает в себя различные настройки, которые влияют на наклон режущей кромки. Как упоминалось выше, более положительный наклон, который присущ для более крутой спирали стружечной винтовой канавке, имеет множество преимуществ. Во-первых, производители используют переменный шаг режущей кромки, как еще один способ борьбы с вибрацией. Слишком сильная вибрация приводит к ослаблению инструмента. Также существует техника, называемая “ski-flute” которая заключается в изготовлении дополнительной выемки за режущей кромкой, которая обеспечивает более острый угол режущей кромки с сохранением прочности инструмента.
Некоторые производители изготавливают внутри стружечной винтовой канавки измельчители стружки, что дополнительно помогает процессу резания.
Что же до фаски и радиуса угла. Подобные конструкционные особенности продлевают срок службы инструмента и могут также улучшить качество поверхности.
Мы едва коснулись темы геометрии концевых фрез, но уже должно быть понятно, что это очень сложный вопрос. Подобная сложность преимущественно определяет высокие затраты производства таких фрез. Добавление всех этих умных функций означает, для производства каждой концевой фрезы требуется полноценный заточный ЧПУ станок. И чем сложнее функциональность фрезы, тем сложнее и дольше будет ее обработка. Микрозаточка режущих кромок это еще один вид обработки, который можно рассматривать как дополнительную отдельную геометрию фрезы, создание которой, в свою очередь, дополнительно удлиняет время необходимое для заточки. Заточить современную концевую фрезу с помощью ручного точильного инструмента практически невозможно, а если вы все же попробуете, то с большой вероятностью уничтожите начальную экзотическую геометрию фрезы.