Командой Darxton решено представить на обозрение общепринятые практики, позволяющие учитывать технологичность и стоимость при проектировании детали.
ЧПУ станки, обычно используемые для создания геометрических форм, требуемых клиентами, - это вертикальные фрезерные станки, горизонтальные фрезерные станки и токарные станки.
Чтобы успешно изготовить деталь на ЧПУ станке, используются определённые программы для определения движений станка.
Запрограммированные инструкции кодируются с использованием программного обеспечения автоматизированного производства (CAM) в сочетании с моделью автоматизированного проектирования (CAD), предоставленной заказчиком. Модель CAD загружается в программное обеспечение CAM, и траектории движения инструмента создаются на основе требуемой геометрии изготовленной детали. После определения траекторий инструмента программное обеспечение CAM создает машинный код (G-код), который указывает станку, с какой скоростью он должен двигаться, с какой скоростью поворачивать заготовку и / или инструмент, а также местоположение перемещения в 5-осевой системе координат
Сложные цилиндрические формы можно изготавливать более экономично на токарном станке с ЧПУ по сравнению с 3- или 5-осевым фрезерным станком с ЧПУ. В чем же разница? На токарном станке с ЧПУ режущие инструменты неподвижны, а заготовка вращается. В свою очередь, на фрезерном станке с ЧПУ инструмент вращается, а заготовка зафиксирована. Для создания геометрии компьютер с ЧПУ на борту управляет скоростью вращения заготовки, а также перемещением и скоростью подачи стационарных инструментов, необходимых для изготовления детали. Если квадратные элементы необходимо создать на круглой детали, сначала создается круглая геометрическая форма на токарном станке с ЧПУ, а затем квадратные элементы будут созданы на фрезерном станке с ЧПУ.
Поскольку компьютер управляет движением станка, оси X, Y и Z могут перемещаться одновременно, создавая ряд функций, от простых прямых линий до сложных геометрических форм. Некоторые ограничения действительно существуют в обработке с ЧПУ, и не все формы и элементы могут быть созданы даже с учетом достижений в области инструментов и средств управления ЧПУ. Об этих ограничениях мы поговорим немного позже.
Свободные допуски
Если заказчик не предоставил чертеж или спецификацию, компания может предоставить общие спецификации, которым необходимо следовать при производстве модели. Эти спецификации могут меняться от одной компании к другой. Кроме того, некоторые компании не имеют стандартизированных допусков и требуют, чтобы заказчик предоставил спецификации.
Ниже перечислены спецификации, которым следует Darxton, если заказчик их не предоставил:
•Допуск для всех размеров будет составлять ± 0,127 мм для всех металлических деталей и ± 0,254 мм для всех пластиковых деталей.
•Если резьбовые отверстия не указаны в предоставленном чертеж, они не будут добавлены к детали и будут обработаны до диаметра, указанного в модели.
•Обработка поверхности (дробеструйная очистка, анодирование, порошковое покрытие и т. д.) не будет применена, если иное не оговорено заказчиком.
•Для металлических деталей толщина стенок должна быть не менее ~ 0,75 мм.
•Для пластиковых деталей толщина стенок должна быть не менее ~ 1,5 мм.
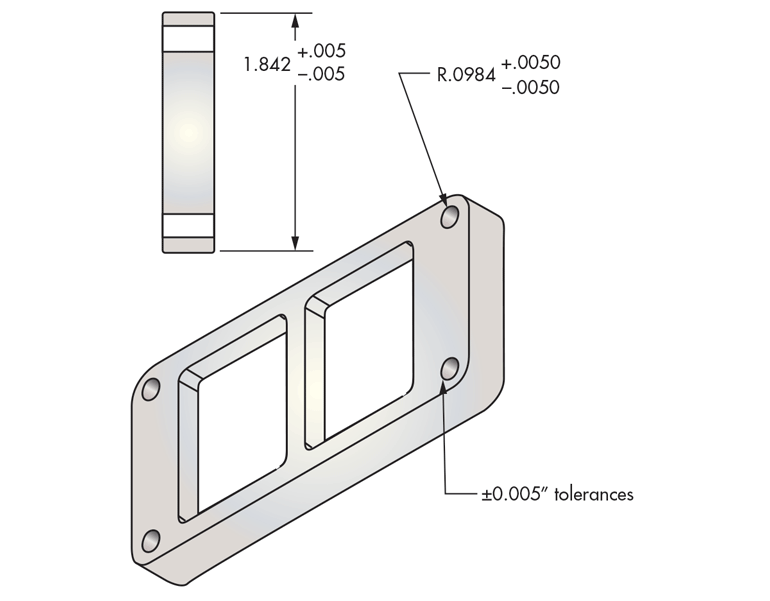
Допуски деталей
Допуск - это допустимый диапазон для размера, который определяется разработчиком на основе формы, посадки и функции детали. Важно помнить, что более жесткий допуск может привести к дополнительным расходам из-за увеличения количества брака, дополнительных приспособлений и / или специальных измерительных инструментов.
Более продолжительное время цикла также может увеличить стоимость, если станку необходимо замедлить работу, чтобы обеспечить более жесткие допуски. В зависимости от обозначения допуска и связанной с ним геометрии, затраты могут быть более чем вдвое выше, чем при соблюдении стандартного допуска. Более жесткие допуски следует использовать только тогда, когда это необходимо для соответствия критериям проектирования детали.
Кроме того, к чертежу детали могут применяться общие геометрические допуски. В зависимости от геометрического допуска и типа применяемого допуска стоимость может возрасти из-за увеличения времени проверки.
Наилучший способ применения допусков - это применение жестких или геометрических допусков только к критическим областям, что поможет минимизировать затраты.
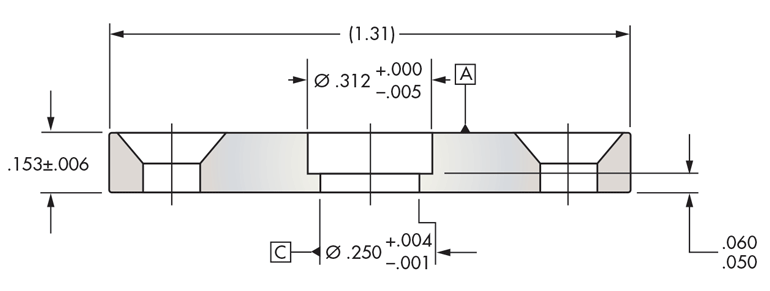
Ограничения по размеру
Фрезеровка
Размер детали ограничен возможностями машины и глубиной резания, необходимой для элемента детали. Обращаем Ваше внимание, что размеры пространства для сборки не соответствуют размеру детали. Например, ход по оси Z в 96,5 см не означает, что деталь можно обрабатывать до такой глубины или высоты. В зависимости от размера детали и элемента, который необходимо обработать, высота Z детали должна быть меньше 96,5 см из-за зазора инструмента и глубины резания. Характеристики и размер детали будут определять обрабатываемую высоту детали.
Токарный станок
Возможности токарного станка будут зависеть от места для сборки или диаметра и длины. Компания также может предложить токарный станок с приводным механизмом, который значительно сокращает время выполнения заказа и увеличивает количество деталей, которые можно обрабатывать, комбинируя дополнительные функции фрезерования с ЧПУ в токарном станке.
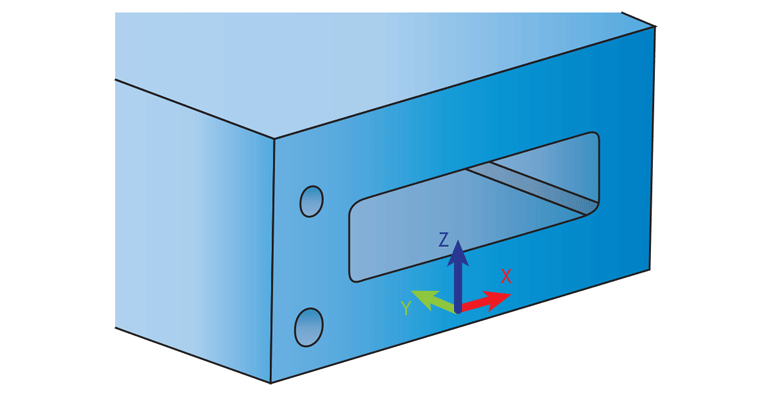
Выбор материала
Выбор материала имеет решающее значение для определения общей функциональности и стоимости детали. Дизайнер должен определить важные характеристики материала конструкции - твердость, жесткость, химическую стойкость, способность к термообработке и термическую стабильность, и это лишь некоторые из них.
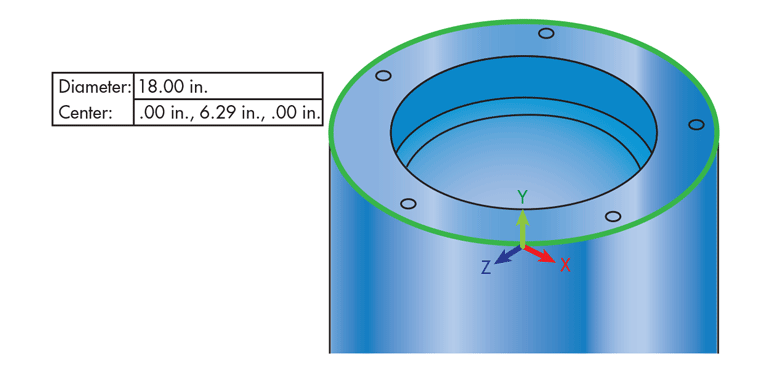
Металлы
Как правило, более мягкие металлы, такие как алюминий и латунь, а также пластмассы, легко обрабатываются, что, в свою очередь, сокращает время и затраты. Более твердые материалы, такие как нержавеющая сталь и углеродистая сталь, должны обрабатываться с более медленными оборотами шпинделя и скоростью подачи станка, что приведет к увеличению времени цикла по сравнению с более мягкими материалами. Как правило, алюминий обрабатывается примерно в четыре раза быстрее, чем углеродистая сталь, и в восемь раз быстрее, чем нержавеющая сталь.
Тип материала является решающим фактором при определении общей стоимости детали. Например, пруток из алюминия 6061 дешевле алюминиевой пластины, а пруток из алюминия 7075 может быть в несколько раза дороже, чем пруток 6061. Стоимость нержавеющей стали 304 может быть в два-три раза выше, чем у алюминия 6061, и примерно в два раза больше, чем у углеродистой стали 1018.
В зависимости от размера и геометрии детали стоимость материала может составлять значительную часть общей стоимости детали. Если конструкция не гарантирует свойств углеродистой или нержавеющей стали, подумайте об использовании алюминия 6061, чтобы минимизировать материальные затраты.
Пластмассы
Пластик может быть менее дорогой альтернативой металлу, если конструкция не требует жесткости металла. Полиэтилен легко обрабатывать, и он стоит дешевле алюминия 6061. Обращаем Ваше внимание, что в зависимости от геометрии, детали из пластмасс могут деформироваться после обработки из-за напряжения, создаваемого при удалении материала.
Сложность и ограничения
Чем сложнее деталь, что означает контурную геометрию или несколько граней, которые необходимо вырезать, тем дороже это будет по отношению к дополнительному времени настройки и времени для резки детали. Когда деталь можно резать по двум осям, наладка и обработка могут выполняться быстрее, что сводит к минимуму затраты.
Для простых двухосных деталей при перемещении инструмента вокруг детали будет удалено больше материала, чем с фигурной деталью. В случае более сложной детали некоторые области необходимо будет вырезать, перемещая оси X, Y и Z вместе.
Чтобы создать сложную поверхность с хорошей обработкой поверхности, необходимо использовать очень маленькие надрезы. Это увеличивает время и, следовательно, цену детали. Общее правило, помогающее минимизировать затраты, - это пробовать проектировать с использованием только двух осей, но это не всегда возможно, если требуется определенный внешний вид или функциональность. Согласование параметров, таких как внутренние радиусы углов и резьбовые отверстия, также поможет сэкономить время и деньги на деталях, уменьшив необходимость в смене инструмента.
Пятиосевая обработка
Возможности пятиосевой обработки позволяют изготавливать более сложные детали наиболее экономичным способом. Пятиосевая обработка означает, что станок и деталь можно перемещать пятью способами одновременно вокруг нескольких осей. Скоординированное движение позволяет более эффективно изготавливать очень сложные детали, поскольку оно минимизирует переналадку, обеспечивает более высокие скорости резания, генерирует более эффективные траектории движения инструмента и обеспечивает лучшее качество обработки поверхности.
Благодаря использованию пятиосевой технологии по сравнению с традиционной трехосевой обработкой, требуется меньше настроек для создания детали со сложной геометрией. При трехосном фрезеровании фасонные детали или детали с обработкой на нескольких гранях требуют нескольких настроек для создания геометрии. Часто при трехосной обработке необходимо изготавливать сложные приспособления, чтобы удерживать деталь в ориентации, необходимой для создания элемента. Пятиосевая обработка исключает необходимость и, следовательно, затраты на создание приспособлений, поскольку деталь можно удерживать один раз и вращать для создания сложной геометрии.
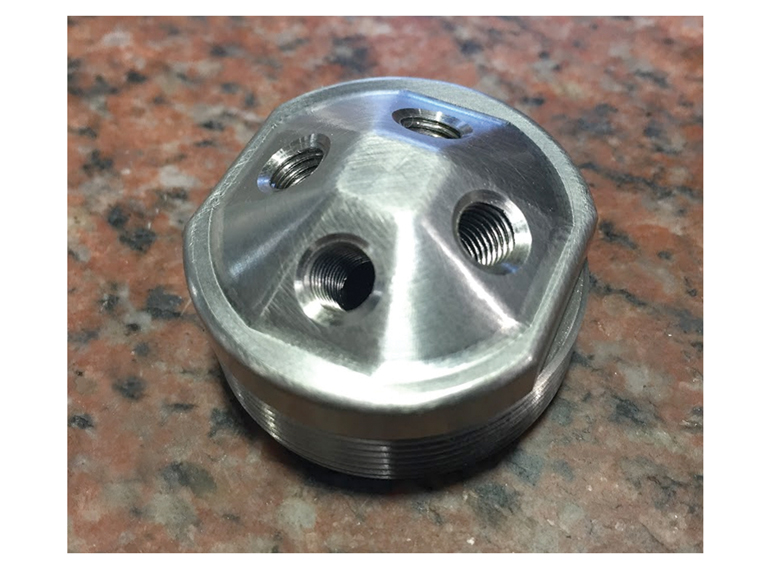
Пять из шести граней могут быть обработаны (с использованием пятиосевой технологии) с помощью одной установки, что исключает затраты и время на создание четырех других установок для создания элементов. Деталь настраивается один раз, и станок с ЧПУ вращает деталь в правильной ориентации для создания геометрии.
Наконец, при использовании пятиосевого станка движение станка и детали позволяет режущему инструменту оставаться касательным к режущей поверхности. Сокращение времени цикла и затрат достигается за счет того, что с каждым проходом инструмента можно снимать больше материала, а также улучшается качество поверхности за счет использования возможностей пяти осей на контурной геометрии. При традиционной трехкоординатной обработке необходимо использовать очень маленькие пропилы для получения хорошего качества поверхности, что приводит к увеличению времени выполнения заказа.
Множество других факторов, которые повлияют на стоимость, время и простоту изготовления.
Во второй части этого руководства (которая появится в ближайшем времени) мы рассмотрим такие особенности, как скругления, брак, виды резьбы, и многое другое.