Доброго времени суток, уважаемые читатели. С сегодняшнего дня мы решили запустить целый цикл статей посвящённый фрезеровки и обработки различных видов металлов и не только. В данный цикл войдут статьи,которые будут полезны как новичкам, так и более опытным мастерам.
Часть 1. Общие понятия о процессе резанья металлов и основные параметры резцов.
1.1 В чем заключается процесс резки и как он происходит?
Основными видами механической обработки металлов являются: точение, строгание, сверление,фрезерование, шлифование и др. Все эти виды обработки осуществляют на металлорежущих станках с помощью различных режущих инструментов — резцов, свёрл, фрез и др. Основой всех разновидностей процесса резания является точение, а основой всех видов режущего инструмента — токарный резец.Процесс резания металлов заключается в срезании с заготовки лишнего слоя в виде стружки с целью получения детали требуемой формы, размеров и классов шероховатости обработанных поверхностей.
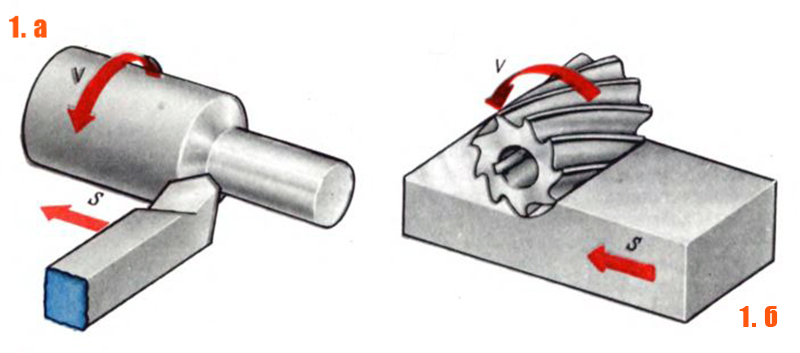
Для осуществления данного процесса необходимо иметь два движения — главное (рабочее) и движение подачи. Главное движение при точении — это вращательное движение обрабатываемой заготовки (рис. 1, а). При фрезеровании главным движением является вращение фрезы (рис. 1, 6). Скорость главного движения определяет скорость резания.
Поступательное перемещение резца в продольном или поперечном направлении является движением подачи при точении. При фрезеровании движением подачи является поступательное перемещение обрабатываемой заготовки в продольном, поперечном или вертикальном направлениях. Скорость главного движения всегда больше скорости движения подачи. В процессе резания образуется стружка.На рис. 2 вы можете видеть наглядную схему образования стружки при резании материалов. Заготовка и резец закреплены на станке. Резец, установленный на некоторую глубину резания, перемещается под действием силы, передаваемой станком.
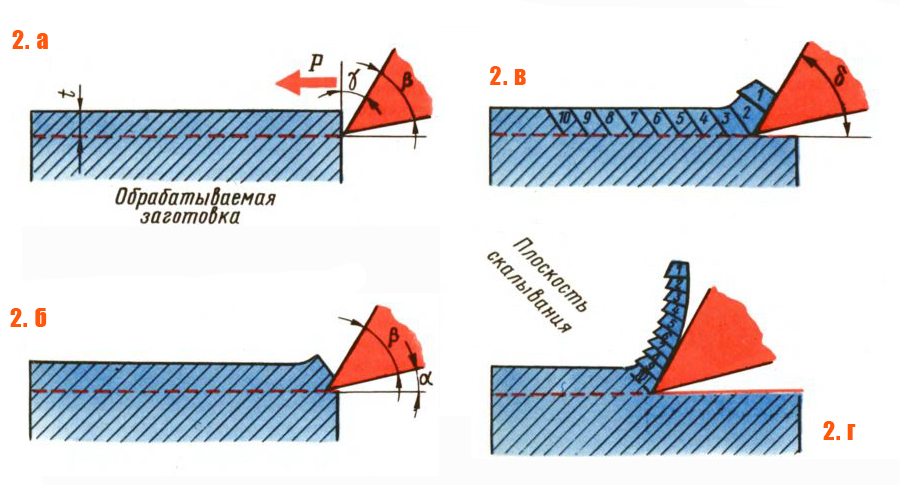
При резании пластичных материалов различают 4 следующие фазы образования элемента стружки. В начале резания происходит соприкосновение резца с обрабатываемой заготовкой (рис. 2, а). Затем резец своей вершиной вдавливается в материал (рис. 2, 6), из-за чего на нём происходит деформация сдвига.
Дальнейшее внедрение резца преодолевает силы сцепления между отделяемым слоем заготовки и основным материалом и приводит к скалыванию (или сдвигу) первого элемента стружки (рис.2, в).
После чего резец, продолжая своё движение, отделяет от основной массы заготовки последующие элементы стружки (второй, третий и т. д.).
1.2 Основные параметры резцов
В металлообработке резцы являются простейшими и наиболее распространёнными режущими инструментами.
Теперь давайте по подробнее разберёмся, что он из себя представляет. Токарный резец состоит из головки (основной рабочей части) и державки. «Державка, что это?». Данная часть резца служит для его закрепления в резцедержателе, установленном на суппорте станка. Основными параметрами державки являются:
Н - высота
B - ширина
L - длинна
Для выполнения определённого ряда задач могут так же применяться резцы с державками круглого сечения.
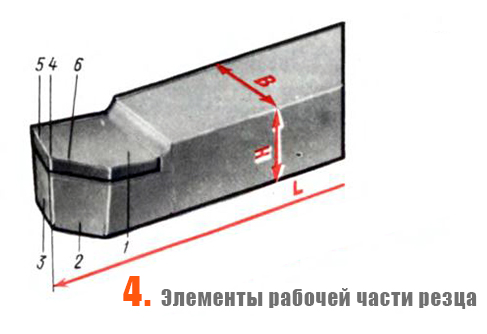
Головка резца образуется специальной заточкой и состоит из
следующих элементов: передней поверхности (грани), задних
поверхностей (граней), режущих кромок и вершины (рис. 4).
Передней поверхностью «1» называют поверхность, по которой
сходит стружка.
Задними поверхностями называют поверхности, обращенные к
обрабатываемой заготовке. У резцов их две — главная «2» и вспомогательная «3». Режущие кромки образуются пересечением передней и задних поверхностей. Их также две главная и вспомогательная.
Главная режущая кромка «6» образуется пересечением передней и
главной задней поверхностей. Она выполняет основную работу резания.
Вспомогательная режущая кромка «5» образуется пересечением
передней и вспомогательной задней поверхностей.
Вершиной резца «4» называется место сопряжения главной
режущей кромки со вспомогательной.
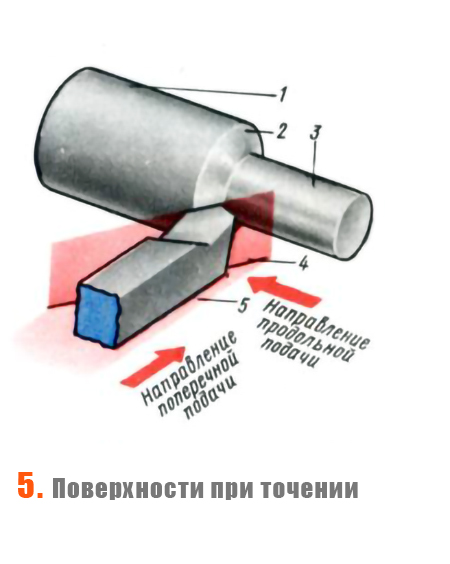
На обрабатываемой заготовке в процессе резания различают следующие поверхности
(рис. 5): обрабатываемую «1», обработанную «3» и поверхность резки «2»
Обрабатываемой поверхностью называется поверхность, подлежащая обработке.
Обработанной поверхностью называется поверхность,полученная на заготовке после снятия стружки.
Поверхностью резки называется поверхность, образуемая на
обрабатываемой заготовке непосредственно режущей кромкой инструмента.
1.3 Как определить угол заточки резца?
Для определения углов заточки режущего инструмента устанавливают координатные (исходные) плоскости: основную
и плоскость резания.
Основной плоскостью «5» на рисунке 5 называется плоскость,
параллельная продольной и поперечной подачам. У токарных Резцов с призматическим сечением державки за основную плоскость принимают нижнюю опорную поверхность резца.
Плоскостью резания «4» называют плоскость, перпендикулярную
основной плоскости и проходящую через главную режущую кромку резца.
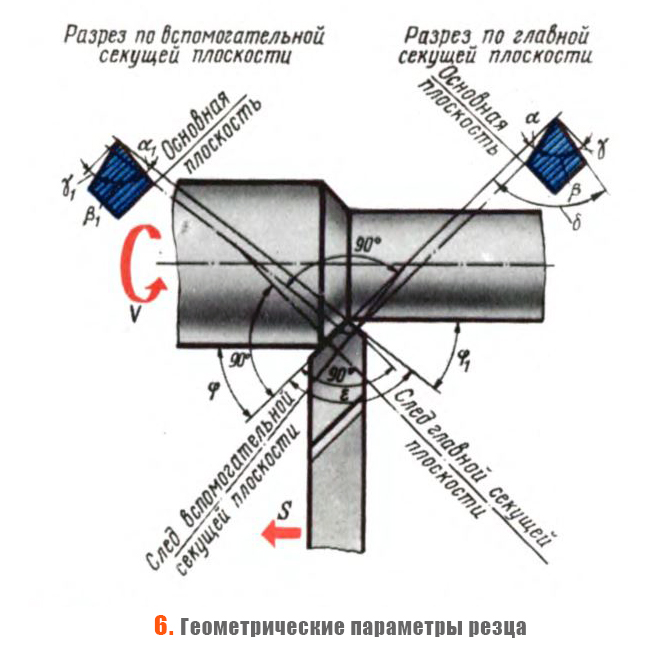
Главные углы резца измеряются в главной секущей плоскости,
перпендикулярной проекции главной режущей кромки на основную плоскость (рис. 6).
Главный заданный угол «α» — угол между касательной к главной
задней поверхности резца в данной точке режущей кромки и плоскостью резания. Задний угол нужен для того, чтобы уменьшить трение задней. поверхности инструмента об обрабатываемую заготовку. Он выбирается обычно в пределах от 2 до 12°.
Угол заострения «β»— угол между передней и главной задней поверхностью резца. От этого угла зависит прочность режущей части инструмента.
Передний угол «γ» — угол между передней поверхностью резца и
плоскостью, перпендикулярной плоскости резания и проходящей через главную режущую кромку резца. Этот угол необходим для уменьшения силы резания, а также для уменьшения трения сходящей стружки о переднюю поверхность резца. При обработке вязких металлов передний угол выбирается в пределах от 10 до 20° и более. При обработке сталей, в особенности твёрдыми сплавами,
передний угол выбирается близким к нулю или даже отрицательным. При работе фасонными инструментами (фасонными резцами, фасонными фрезами, резьбовыми фрезами, зуборезным инструментом и др.) передний угол должен быть равным нулю либо
Иметь небольшие положительные значения (от 2 до 4”).
Вот мы и освежили знания по основам резки, которые помогут нам лучше понять различные тонкости и спецификации фрезеровки, с которыми вы сможете ознакомиться в данном цикле